Return
to Technical Article Directory
Return to BRE
Home
Page
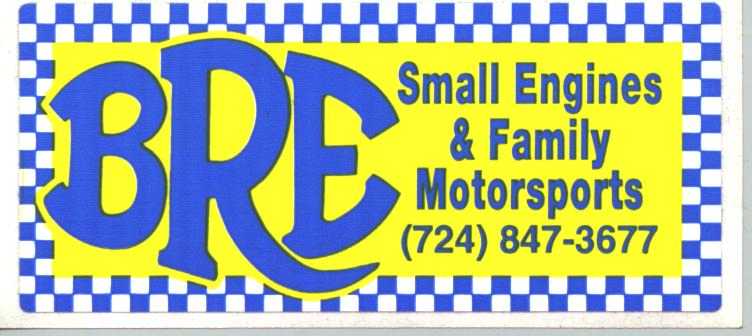
Rebuilding the Rotary Valve 2-Stroke Cycle Engine
...a cost-effective way to go real fast!
by Mark Bergfelt
This is the manuscript of the article published in the June 1995 issue
of National Kart
News.
There have been some additions to the original text. These
additions are in (parenthesis).
Contact National
Kart News to purchase a copy of this publication complete with
illustrations.
When TKM first started importing engines to
the United States, three of my old kart racing buddies were among the
first to run them. Ed Hudock and Mitchell Matchett were the drivers and
Russ Matchett was the owner. At the time there were still a lot of
McCulloch 10ls running competitively in the open classes and I was
among the racers still using them. To make a long story shorter, Hudock
could not make it to some races due to a serious injury, my kart was
not working right and Matchett asked me if I would like to use Hudock's
kart for the day. I did, but maybe I shouldn't have. I was addicted
immediately. 147+cc of raw horsepower:' Awesome! Totally
unexplainable. You have to try it.
It's only natural for a new driver to want to
go faster, and there are a variety of options available to that driver
who wants to step into a quicker ride, all of which are possibilities
for articles in this magazine: At the far end of the performance
spectrum is the 150cc Open 2-cycle Class, as it is referred to by IKF,
or the Unlimited 2-cycle, as WKA calls it, or Outlaws, as some
nonsanctioned Midwestern tracks have referred to the division, or
the Unlimited All-Stars, as it is known in my neck of the woods. On all
but the tiniest of dirt bull rings, and a lot of those too, these are
the quickest rides around.
The Unlimited Class isn't always the biggest class at a racing event,
but it is always very fast and draws a lot of attention. It is
certainly not a cheap class, to get involved with (initially),
but after comparing initial purchase and maintenance prices to
those of running an all-out Open Briggs, Unlimited 2-cycle is a very
cost-effective way to go real fast. Intelligent upkeep is
necessary to make that statement true. Mistakes can be costly.
The axle clutch has also helped to make this
class more affordable and less maintenance intensive. It has all but
eliminated the expense created by making a tuning error with an
engine clutch, which almost always resulted in destroying that costly
component. Sure, axle clutches are expensive up front, but they're one
of the best values in racing. The only thing I've had to buy for my
5-year-old Horstman axle clutch is oil! Prior to using an axle clutch,
most of the race to race maintenance involved removal and inspection of
the engine clutch. What drudgery, Engine clutches are also responsible
for many of the "horror" stories associated with the "big block"
2-cycles. Not having to perform this time consuming chore has added to
the fun factor of karting, which is most important.
(Since this article was published, it has become very popular to
install a timing belt pulley on the engine. The timing belt,
usually 30mm wide, is very durable and is used to drive a
jackshaft. In many cases, the jackshaft is rotated at 1/3 the
speed of the engine shaft. This puts the rpm in the range of the
clutches used for stock 4-cycle racing. A clutch of this type is
installed on the output end of the jackshaft. This set-up has
proven to be, reliable, relatively inexpensive, and very fast.)
This article will outline the procedures for
maintenance, and rebuilding of engines that started their existence as
l35cc rotary valve engines, I say "started" because many of these wind
up being 150+cc beasts. Most of the procedures will apply to 100cc
rotaries, reed and piston port engines as well.
The first step in rebuilding the engine is
removing all of the external accessories, such as the drive sprocket or
engine clutch, air filter, mounts and so on. Before taking any wrenches
to the engine, though, a thorough cleaning of the, entire assembly is
recommended. Toiling on a grimy, dirty motor is not pleasant, but
working on a clean, exotic, foreign power plant can be much more
enjoyable.
The starter nut can be removed at this time. I
prefer to use an air or electric impact wrench to remove this item,
Using this method eliminates the need to lock the crankshaft to remove
the nut. Many methods of locking the crankshaft can cause it to be
twisted out of alignment. Remove the third bearing support cover. A 5mm
hex key /wrench is usually what will get the screws out that hold the
cover on. Next, remove the extension shaft. You will need a motoplat
wrench or a large adjustable wrench to hold the rotor while using
another adjustable wrench or open end wrench to unscrew the extension
shaft. These are usually very tight, so watch your knuckles. Use a
motoplat rotor puller to get the ignition rotor off. These are
available from most kart shops that deal with 2-cycle engines. Before
removing the ignition stator, use a center punch to mark the stator and
crankcase so that you can get the ignition timing set where it was.
That's mainly a precaution to take if you don't know what the ignition
timing dimension is. It also gives you a baseline for a setting that
works if you want to experiment with ignition timing. We'll cover
the topic of ignition timing when we put the engine back together.
PRESSURE CHECK ENGINE
Before opening up any racing 2-stroke cycle
engine, it is very wise to pressure check it, especially if it is doing
weird things like not shutting off, even when you choke it violently,
or it won't idle down when you get off of the throttle, or it gets real
hot and the carburetor screws are turned out so far they are ready to
fall out and there is little pop off pressure. Engines are literally
air pumps that also burn fuel, so the more efficiently they can pump
air, the better they are going to work. If there is an air leak
anywhere in the engine, the suction pulses created by the piston
moving upward will pull air in through the leakage point, causing
the problems mentioned above and worse. It is so important that
2stroke crankcases hold pressure and vacuum, that regular pressure
testing should be part of the maintenance program on all racing engines
of that type. To perform the test, you will need to have some type of
hand air pump, hooked up to a pressure gauge. Azusa Engineering makes a
unit that checks both pressure and vacuum. Walbro and Tillotson both
make units for testing carburetors that can be used. I prefer my
homymade version of the tool that has served me well for at least the
past 18 years (28 as of the date this was posted to my web
site). I was lucky enough to have an acetylene gauge, an old
bicycle tire pump, a brass brake line fitting and a fuel fitting fuel
petcock and some fuel line laying around in various corners of the
garage at a time when I had no cash. The tool was originally intended
for temporary use until I could get a better one. However, I could
never find what I thought was a better one. The most critical thing to
be concerned with when putting such a device together is making sure
that it does not have any leaks around the fittings. The tool needs to
be checked by plugging up the outlet tube and pumping it up. Shut off
the inlet valve and stick it in water. If there are no bubbles, you're
in good shape. If there are any leaks, fix them now.
Now that you have a pressure checking tool,
you will have to block of the exhaust port and intake port where the
carburetor bolts on. A,II you need is an old inner tube. Cut out some
pieces of the rubber just big enough to replace the exhaust header and
carburetor gaskets, but don't cut out the holes in the middle. Remove
the carburetor and header, and install these rubber inner tube gaskets.
Reinstall the carburetor and header. If you want to get fancy, you
can cut out and drill metal block off plates for pressure checking your
engine. You will now need a fitting to pump air into the engine. You
could install a fuel hose fitting on one of your block off plates.
Azusa Engineering makes a nice fitting for hooking up your air hose to
the spark plug hole. You can also make your own. by using an old spark
plug shell. You have to break out the porcelain and thread the hole in
the center of the plug. It's easier to buy one, but a lot of guys have
more time than money, so it's nice to know that this is another item
the do-it-yourselfer can make. I had to weld the hole shut and redrill
it to get the size hole I wanted.
Install your fitting, hook up your hose and
you're ready to go. Pump air into the engine until the gauge reads 8 to
10 pounds. Shut off the Petcock. The gauge pressure should hold
indefinitely. If the pressure drops, you have a leak. If it is a bad
leak, you may be able to hear and even feel it. Brush some water and
detergent solution on the suspected area to verify the situation. Slow
leaks are tougher to find. Brush the leak detector solution all over
the engine and look for bubbles. Sometimes it may be necessary to dunk
the entire engine in a stationary laundry tub filled with water to find
the leak. Remove the ignition components before doing this. It
would be wise to use a block off plate instead of the carburetor before
giving the engine the dunk treatment. Make a note of any leaks that are
found, and make sure that repairing them is part of the rebuild
process. All types of things can cause air leaks. Remove everything you
put on to pressure check the engine and it's time to move on.
It is often advisable to check the engine for vacuum leaks as well.
Azusa's deluxe tool does this, as well as the vacuum pumps available in
auto parts stores. I have been able to solve all of the leak-related
problems that I have encountered by simply using pressure.
CHECK THE END PLAY
At this point I like to check the crankshaft
end play. It's a good idea to measure it now because if there is too
much we can shim the crankshaft bearings when we change them, but we
need to know now, while the engine is together. To check the end play,
attach a dial indicator to one end of the crankshaft so that the
plunger contacts the side of the crankcase. There are a number of ways
of attaching the indicator to the end of the shaft. I made a device
from an old starter nut that allows the indicator to be bolted in
place. The next step is to pull on the crankshaft length wise. While
holding the shaft, zero the dial indicator. Next, push the shaft firmly
the other way. Check the dial indicator. The reading will be the
end-play in thousandths of an inch. Record your measurement for future
reference. Remove your dial indicator and proceed with the teardown.
At this point you may remove the cylinder head
or the rotary valve cover. We'll proceed with the rotary valve cover,
or intake manifold, as some call it. Your 5mm hex key will probably get
the screws out. Gently tap the cover with a plastic tipped hammer to
jar it loose and remove the cover. Push out or pry the oil seal from
the cover and remove the gasket. Hopefully, the rotary valve did not
fall on the floor when you took the cover off. Use some nail polish or
automotive brush-on touch-up paint to mark the rotary valve and
crankshaft to make sure you get it back on in the right position. On
many engines it can go on in six possible positions, but only run right
in one of them. It is very satisfying to get it right the first time,
but very frustrating the other five ways.
The cylinder head comes off next. There are
various sizes of stud/nut combinations used to hold the head on. Ones
that require a l3mm or 16mm wrench are the ones most familiar to me. A
socket wrench with a ratchet and extension will work here. TKM engines
have two additional screws that come off with a 6mm hex key. After
removing all nuts and screws, pull the head off. On the majority of
engines, you can pull the cylinder off now. On others, a few more nuts
need to come off first.
Some people (actually most engine
builders) refer to the cylinder as the "jug." You may need to provide
some gentle persuasion with a plastic tipped hammer to jar the gasket
seal loose. Measure the thickness of the cylinder base gasket with a
dial caliper or micrometer. You will need to obtain a new one of the
same thickness before you put the engine back together.
The piston is the next candidate for removal. It would be a good idea
to get a pair of safety glasses for this next operation. Removal of the
piston pin clips ranges from simple to difficult, depending on what
type you have. The "rabbit ear" type are easiest. Needle nose pliers
make short work of those, but they still have a habit of slipping off
of the pliers and sailing off to some hidden corner of the shop. Spiral
lock clips are tougher. Start fishing them out with a scratch awl or
other thin tool. Good luck. There's also clips that have no ears to
grab with pliers.
It is best to use a piston pin removal tool to
get the piston pin (wrist pin) out. MISI makes one that works
real well. The tool reduces the risk of bending the connecting rod
while removing the pin. The special tool is not absolutely necessary.
If the piston is adequately supported, a large flat punch will do the
job, but it is important not to stress the rod from the side. When you
remove the pin, regardless of the tool, lay a rag on the bench to catch
the wrist pin bearings. That step is important if you have loose
rollers or don't know what's in there. I recommend the use of the caged
type top end bearing that is used in K-30 Komets in all of the big
2-strokes. Once the pin is out, the piston falls right out. Be gentle
with it if there's a chance you might use it again, even though you
probably shouldn't.
Get your 5mm hex key wrench and remove
the screws that hold the crankcase halves together. Gently tap on the
case halves with your plastic hammer. Once they're apart the
crankshaft/connecting rod assembly can be removed.
CRANKSHAFT REBUILDING
Crankshaft rebuilding requires special tools
that most people don't have and probably won't use very often, so
it is advisable to have the crankshaft rebuilt by a reputable kart
or even motorcycle shop. Truing a built-up crankshaft is an art and
requires practice and patience. The procedure wil1 be explained
next. The reader may want to give it a try (If you screw it up, send it
to BRE to get it straightened out. After all, fixing engines is a
big part of how we earn our living.), or should at least know what he
is paying for.
Before rebuilding the crankshaft, measure the
width of the assembly at the crankpin. The width of the crankshaft
affects the endplay. If you arbitrarily change the width somewhat,
you will need to compensate when installing the main bearings. To
rebuild a built up type crankshaft, the crankpin must be
removed. This is accomplished by using a crankshaft splitting plate and
splitting cylinder, a push pin and a hefty hydraulic press. Set up the
splitting cylinder and plate so that the crankpin is located
at the center of the splitting plate. Be sure to locate the connecting
rod so that it protrudes from the slot in the splitting cylnder.
Set up the splitting cylinder in the press so that you can use the push
pin to push the crankpin out of one-half of the crankshaft. After doing
that, remove the thrust washers, connecting rod and big end bearing
from the crankpin. Flip the side of the crankshaft with the pin
remaining over and set it up on a plate in the press. Using the pushing
pin, press out the crankpin.
Carefully inspect the connecting rod for any imperfections. You don't
want to replace this part unless you really have to because it can be
very expensive, but if it isn't in perfectly serviceable condition,
don't risk trashing an engine with a marginal rod. It should also be
checked for straightness by using a surface plate, parallel bars and
pins that have been machined to a close fit of the bores of the big end
(bottom) and little end (piston pin end) of the connecting. Insert
the pins in the rod and set it on the parallel bars. It should sit
perfectly flat. Then lay it flat on the plate to see if it lies flat. A
twisted or bent rod can be straightened using specially made
tooling. It is highly advisable to take the rod to an automotive
machine shop that has magna flux testing equipment and get the rod
checked. While you're at it, take the crankshaft halves and get them
checked too.
Before pressing the crankshaft back together, obtain a new crankpin,
bearing assembly, and thrust washers. Lay one crankshaft half on a
plate on the press and carefully press the pin into the hole from
the inside out. Apply some good quality grease on a thrust washer and
put it on the pin. Grease up the new bearing assembly and place it on
the pin and install the connecting rod over the pin. Install the
second thrust washer. Carefully place the other crankshaft half on the
pin, align them up close by eye and place the parts in position in the
press. Press the crankshaft on the pin just enough that they will stay
together. Remove the assembly at this point and check to see that
they are closely aligned. A square laid across the crankwheels will
help with the check. Use a brass hammer to smack the crankshaft
halves into alignment. Place the crankshafcassembly back in the
press and press it all the way together. If you have the right pin, the
rod will rotate free and smooth on the pin but it will not be sloppy.
Now comes the tedious part - aligning the crankshaft. You will need two
v-blocks and a surface plate or the centers of a lathe or a truing
fixture. The main criteria of these tools is that they are perfectly
rigid and stationary. I prefer to use myoid faithful South Bend
lathe. You will also need two dial indicators and the necessary
fixtures to mount them in place. Position the indicators so that they
contact the main bearing journals of the crankshaft. This setup will
allow you to check the run-out of the journals. To check the run-out,
rotate the crankshaft using the connecting rod. Check to see the
highest reading on the dial indicators. Zero the indicators at that
point. Rotate the crank again and check your indicators. If the one
needle rises while the other falls, and the crank halves are twisted
about the crankpin, they are not concentric. This is called
vertical misalignment. If this is the case, remove the crankshaft
assembly from the centers and smack the crankwheel where it aligns with
the high reading dial indicator. Use a large brass hammer and hit it
hard. If the needles rise and fall together, the flywheels are not
parallel. This is called horizontal misalignment. If the high point is
on the crankpin side, the flywheels will need to be spread apart. I use
a large modified cold chisel wedge and my brass hammer for this
operation. Insert the wedge between the flywheels and tap. Remove
the wedge and recheck the alignment. If the high point is opposite the
crankpin, the flywheels are spread apart. Use the brass hammer and
smack the outside of one flywheel toward the other and recheck the
alignment. As you can probably imagine, this can become a tedious
production, especially when you realize that the goal is zero
run-out. Those needles on the dial indicators should sit
perfectly still when you are done. Don't be surprised if, after a long
time, you get very close but can't get it right on the money. If the
center lines of the crankpin holes and the center of the halves are not
exactly the same distance apart on both crankshaft halves, perfect
alignment may not be obtainable. This is most likely to occur when a
broken half is replaced. Remember, the closer to perfect you can get on
alignment, the more RPMs and power the engine will make.
LAD makes a fixture for pressing
crankshafts together that is supposed to make this task easier. I have
never used one so I can't comment on its effectiveness. The method I
use is found in every motorcycle mechanics textbook I've ever seen, and
it works.
PROTECT YOUR CRANKSHAFT
Once the crankshaft is aligned, put it away
somewhere where it won't get knocked around. It does not take much to
knock a crankshaft out of alignment. Once it is supported by the
main bearings between the crankcase halves, it will be considerably
more durable. Before you put it aside, though, get your calipers or
micrometer and measure the width of the crankshaft and compare it to
your measurement before rebuilding the crankshaft. If your
crankpins were the same length, then the chances are the measurement
will be the same.
A hot plate can be used to remove the main
bearings from the crankcase halves. Lay one case half on the hot plate
with the bearing opening facing down. Heat the case half up until the
bearing either falls out or can be removed by light tapping with a
flat punch or similar tool. For the next step, get a large pair of
pliers or thick welding gloves because the case half is hot enough to
bum you badly. Remove the case half from the hot plate and lay it on
the bench with the bearing opening facing up. Drop a new, cool,
bearing into the opening. Make sure it goes in straight. (I
am assuming that the case half is squeeky clean to begin with. If
it isn't, make sure that it is before installing the new
bearings. The inside of the engine can't be clean enough.)
Repeat the procedure for the other side. If the rebuilt crankshaft
turned out to be narrower, or if you want to cut down on the amount of
crankshaft end play, drop a bearing shim that is one-half the amount of
space that you want to take up under each main bearing before it is
inserted. Allow the case halves to cool until they are cool enough to
touch with your bare hands.
Apply gasket sealer to the gasket surface
of the case halves and let it get tacky. I prefer Yamahabond No.4. (I
now use Mega O.E.M. Grey Import Gasket Maker that I buy at a local Auto
Zone store.) Slide the magneto end of the crankshaft into
the magneto half of the crankcase. Slide the rotary valve case half
over the rotary valve end of the crankcase. Gently push the two case
halves together, being careful not to apply any force that could cause
accidental crankshaft misalignment. Insert the appropriate screws into
their holes and tighten them in a crisscross fashion. Torque them
to 85 inch pounds. If everything is right, the crankshaft will
revolve smoothly and easiIy.
Now is as good a time as any to
recondition the cylinder. If this is a simple
"freshening-up," the cylinder is probably not damaged and is
only glazed. "Glazed" is a term that refers to the shiny look that the
cylinder gets from the rings rubbing on it. This glaze must be
removed if the new piston rings are to break in properly. A hone is
used to remove the glaze and replace it with a crosshatch finish.
Crosshatch is extremely fine, uniform, crisscross scratches that are
usually about 45 degrees to each other. These scratches give the
2-cycle oil a place to sit, so that it can lubricate and help the rings
seal things up. They also help the rings to seat in and match the
contour of the cylinder better.
In order to ensure that the cylinder is round when the engine is
totally assembled, the cylinder should be sandwiched in a torque plate
for the honing operation. This is most important if a precision ridged
hone is to be used, and it isn't a bad idea even if you are using a
ball-type hone. Spring-type glaze breaker hones are not recommended for
use on racing engines. Follow the directions for the hone that is being
used for best results. Only a few strokes of the hone will be
necessary to restore the crosshatch finish if the cylinder is in
good shape. A cylinder with vertical scratches should be honed until
they are gone. (especially in the area above the exhaust ports.) At
that point the cylinder diameter should be carefully measured and
a piston obtained that corresponds with the resulting oversize.
The cylinder should be finish honed to obtain the clearance recommended
by the piston manufacturer.
After the cylinder is honed, the edges of the
transfer and exhaust ports should be broken (rounded off very slightly)
with a piece of fine emery cloth. This helps the rings to hold up
longer.
DON'T IGNORE THE CYLINDER HEAD
The cylinder head is a relatively simple part
but should not be neglected. Carbon buildup can be removed with steel
wool. The steel wool can also be used to polish the head to a high
gloss. It is harder for carbon to stick to a shiny, slick surface. A
cylinder head turning tool that screws into the spark plug hole of the
head (installed in the chuck of an engine lathe) makes this task easy.
If the head has been dambged by a bearing or some other item
coming apart, the head can be turned in a lathe to restore the surface.
Care must be taken to retain the original contours and head
volume. This article assumes that the head has not been damaged or
the compression ratio is not to be altered.
Many of the foreign rotary valve engines
do not use a cylinder head gasket. You can't blow a gasket that isn't
there and this arrangement ensures good heat transfer between the
parts. In order to ensure a good seal between the cylinder head
and the cylinder, the head can be matched to the cylinder by lapping
the parts. Apply valve grinding compound to the top of the cylinder and
place the head on top of it. Rotate the head on the cylinder like you
were lapping a poppet valve. (4-cycle guys should be really good at
this step.) Wipe off all traces of the valve grinding compound.
Inspect the mating surfaces of both parts. They should both have a
uniform dull gray appearance
.
Proper cleaning of the cylinder is a simple,
but most important step in putting together an engine that will give
maximum service. This is also true of any part that is put into a
precision engine, especially those that have had machine work done on
them. First, parts need to be cleaned in a typical parts cleaning
solvent and blown off with compressed air. Second, (AND MOST IMPORTANT)
the parts need to be scrubbed in a solution of hot water and laundry
detergent. They then need to be rinsed in hot water and then dried
immediately. Lightly oil all ferrous metal parts (iron or steel) so
that they do not rust. It is important not to skip the detergent bath.
This step strips all oily residue and very fine metal shavings from
machined parts, especially cylinders. Most solvents can't completely
strip all residue and particles away. These particles are abrasive
and will cause premature wear of expensive vital parts if left in the
engine. Everything going into the engine should (must)be squeaky clean.
Before installing the rings on the
piston, they must be checked in the cylinder for proper end gap.
Quite often, the engine, ring, or piston manufacturer will specify
the best gap for his or her product. It is wise to follow their
instructions.
To check the gap, place the ring into the cylinder and even it up with
a piston. Measure the gap with a feeler gauge. If it is too small, the
end of the ring will have to be filed carefully until the desired gap
is achieved. If the gap is excessively big, get a larger oversize ring
and file it to the desired gap. Make certain, when filing end
gaps, that the ring fits around the pins properly and without
binding. It is better to have a gap that is a few thousandths too big
than one that is too small, but right on the money is always best.
At this point in the rebuild process, I prefer
to install the piston. Carefully inspect the top end needles, cage
(if so equipped), wrist pin (piston pin), and thrust washers. If any of
these parts are not in perfect condition, replace them as needed.
(Actually, you should always replace these parts when freshening up an
engine. Sure it costs more, but that's a whole lot better than
loosing that $1,000 first place money because a bearing came apart on
the last lap of that big race. When I rebuild an engine,
especially for a customer, I would rather hear complaints about the
price tag for the rebuild, than the complaints that come with an engine
that came apart at a crutial time.) If you are using a loose
needle-type bearing, use white grease (Now I use Sta-Lube Engine
Assembly Lube with moly-graphite, from CRC that is available in auto
parts stores.) to glue the rollers in place in the connecting rod. The
grease can also be used to hold the thrust washers to the side of the
rod while installing the piston. Whenever possible, I prefer to use the
caged type bearing that is used on Komet K-30 engines. With this type
of bearing the grease won't hurt, but a good motor oil is all that is
needed as an assembly lubricant. They're easier to install, and
much easier to deal with if, in case of an emergency in the pits,
piston service becomes necessary.
Put a few drops of engine oil on the piston
pin bores of the piston. Slide the piston in position over the
connecting rod. Carefully slide the wrist pin through the piston and
connecting rod. This operation is much easier if you use a piston pin
tool, such as the one available from MISI.
POSITIONING IS IMPORTANT
Be sure that the piston is not put on
backward. The location of the piston ring pins is most important. A
mistake here could result in a damaged piston or cylinder. Secure
the wrist pin by installing new piston pin clips. Never re-use old
clips and watch your eyes while dealing with those little devils. The
piston pin clips should be installed with the gaps toward the top
of the piston or the bottom, but never to the side. This precaution
will eliminate the piston motion from causing the clips to come out.
Find your new cylinder base gasket. It needs to be the same thickness
as the old one unless you wish to alter the performance of the
engine. Changing the thickness of this gasket will alter the port
timing and the compression ratio. I like to coat the gasket with
motor oil before installing it. It helps it seal by making the
gasket swell slightly and also makes it easier to remove later.
Before installing the cylinder, oil the bore with motor oil (I keep a
bottle of chainsaw/lawn mower 2-stroke oil in a squeeze bottle for that
purpose). This will ensure initial lubrication and keep the
cylinder from rusting if the. engine is not goingt to be used right
away. Slide the cylinder on to it's studs and carefully lower it onto
the piston with one hand. Use your other hand to squeeze the rings
together and slide the piston into the bottom of the cylinder.
I have found that two three-fourth inch wide strips of plastic cut from
an old number plate make a good tool for holding the piston steady
while sliding the cylinder over the piston. The strips should be
four inches long or longer and be placed under the piston, parallel to
and on either side of the rod. After the piston is started into the
cylinder, the strips can be easily slid out. (I don't actually do
this any more. I've done it so much that I personally find it
easier to leave the strips out, but I remember well when it seemed like
I just had to use them.) Carefully slide the cylinder on all the
way. Make sure everything is together right by turning the ends of the
crankshaft. Everything should slide or rotate smoothly.
Crankshaft seals are a very important part of
a 2-stroke cycle engine. A leaking seal can (will) cause disastrous
results. Seal replacement is a mandatory part of a 2-stroke
rebuild, and periodic replacement between rebuilds may be necessary to
prevent expensive failures. Apply motor oil to the lip of the seal
that will contact the crankshaft. (Now I stuff the inside of the
seal with the moly-graphite engine assembly lube.) Apply a thin film of
silicone sealer to the outer edge of the seal. This acts as a
lubricant while installing the seal and ensures that there will be
no leaks around the outside of the seal when it cures. On most
foreign engines the seal can be pressed in with your fingers. One
seal will be installed on the motoplat side of the crankcase, and one
will be installed in the rotary valve cover.
Install your motoplat ignition stator and
rotor at this time. Use the same wrenches that you took it off with. Do
not tighten the stator screws yet. Attach a dial indicator to one of
the cylinder studs. Zero it at top dead center. Turn the crankshaft
backwards until the indicator is between. 0.110 inch and 0.085 inch.
These dimensions are for l35cc engines. Longer stroke engines, like
many Komets, will want timing closer to 0.110 and shorter stroke
engines like TKMs will be happier closer to the 0.085 dimension.
Experiment to get the best results for your engine. (More
advance, ie., 0.110 will give crisp throttle response, good bottom, but
may heat up more. Less advance, ie., closer to 0.085 will give
better top-end or sustained full throttle operation. Much more
can be said on the topic.) With the piston set at the dimension
that you desire, line up the marks on the stator with the rotor, then
tighten the stator screws.
The cylinder head can go on at this point. If
your cylinder head was modified to use an o-ring seal, install a new
o-ring at this time. Some engine builders prefer to wipe a very thin
film of copper-type silicone sealer on the sealing surface of the
cylinder before installing the head. I have done this, and it works,
but it is far better to use none at all than risk using too much.
Install the cylinder nut flat washers. They are easier to get on if you
place them on a small punch or screwdriver and place the tool tip on
top of the stud and allow the washer to slide down the tool onto the
stud. Install the nuts finger tight, then torque them in a crisscross
manner, first to one-third the final torque, then to two-thirds, then
to their final spec. Torque the cylinder stud screws to 200 to 250 inch
pounds (thicker studs use the higher torque). Of course, you'll need to
use a torque wrench.
Apply a coating of motor oil to the surface of
the crankcase that the rotary valve will slide over. Install the rotary
valve, lining up the marks made earlier on the valve and
crankshaft. If you dropped the valve while removing the cover, and
could not figure out where to mark it, install it so that it is closing
as the exhaust port is opening. The events probably won't correspond
perfectly, but they will approximately, usually within 10 to 20
degrees of crankshaft rotation.
DON'T BLOCK HOLES
Apply a coating of motor oil to a new rotary
valve cover gasket. Place the gasket on the cover and be sure that the
carburetor pulse holes are not blocked. Poke a hole through the
gasket if any of the holes are blocked (This should have said,
carefully cut out a small hole with an exacto knife or some similar
tool.). Install the rotary valve cover and screws. Tighten the screws
in a crisscross manner.
Screw on the starter nut as tight as you can
by hand. The electric starter will take care of torquing it down (You
could do that, but torque it down now, just in case). At this point, it
is most important to pressure check the engine as described
earlier. Do whatever is necessary to repair any leaks that may be
found. Install a freshly re-built carburetor. Carburetor
rebuilding and tuning is another article in itself. Set the carburetor
slightly rich for initial start-up and break in.
Many engine builders have different
recommendations concerning what spark plugs to use. I have developed a
preference for NGK B9EGV and BIOEGV plugs. (Since this
article was written I have switched to ND W27ES-ZU (warm), W29ES-ZU,
W31ES-ZU, and W34ES-ZU (coldest) but I still like the NGK.
It is just a little easier for me to get the ND through our supply
channels.) The B9EGV is the warmer of the two and I use it the most. I
prefer the B10OEGV for very hot days. These are fine wire,
goldpalladium type racing plugs. They offer good performance and
resist fouling. Set the gap to .040 inch. I have also used the
equivalent heat range Split Fire plugs and these also work well. (I
have since developed the opinion that these are more of a gimmick but
they do work ok).
Install all of the engine accessories and bolt
the engine assembly to the kart. I can't count the number of times that
I have broken in engines under racing conditions, but it is
advisable to run the engine under a changing load with a rich
carburetor setting for about 15 to 30 minutes before leaning it
down and running it at full tilt. Running a kart on a stand will not do
much to break in an engine. It will simply ensure that the engine does
run. An engine must be under load to exert the right pressure on the
rings so that they break in properly to make full power.
Most of the engines that I build are used for
Saturday night dirt oval type racing. Under that type of condition
I have found that a bottom end can be used safely
for about 10 shows (After using an hour meter on a variety of karts,
the average engine running time for a Saturday night dirt show is about
20 minutes.). After the fifth show, I like to pressure check the engine
before each race as a precautionary measure. I do the same with the
carburetor (check pop-off). By all means, correct any problems as they
are encountered. For good performance, I like to change the rings
after the fifth race. (For IAME engines, Komet, Parilla, etc, you can't
get rings separately so you would have to change the entire piston
assy.)
Although I have pushed engines somewhat
beyond 10 races before a total rebuild, this experience taught me
that 10 is the practical absolute limit. Many engine builders feel
that's too many. (The newer Parillas and similar engines produced
now can safely go a few more shows). After that, don't be
surprised when the main or bottom end rod bearing comes apart,
destroying other parts in the process. That's one of the causes of
the horror stories that are associated with the big rotary valve
2-strokes. Don't misunderstand me here. These engines will take a
beating and perform well, but don't expect the bearings to last
forever. They won't
A 135cc Open rotary valve engine is certainly
not cheap (to buy brand new, initially), but when properly
prepared and maintained, it can provide a cost effectiveway
to go real fast. (It could even wind up costing no more, or possibly
even less to maintian than a top level "stock" class flat head
4-stroker.)
To comment or ask questions about this article contact the author at info@bergfeltracing.com